Needle turn-mill combination precision machining is a specialized machining technique that offers unique benefits and finds applications in various industries. Let's explore the advantages and applications of needle turn-mill combination precision machining:
Benefits:
Versatility: Needle turn-mill combination precision machining provides versatility by combining multiple machining operations into a single process. It integrates turning and milling capabilities, allowing for the efficient production of complex components with a wide range of features, such as contours, pockets, holes, and threads.
Reduced Setup Time: By performing multiple operations in a single setup, needle turn-mill machining reduces the need for multiple machine changes and associated setup time. This results in improved productivity, shorter lead times, and cost savings.
Enhanced Precision and Accuracy: The combination of turning and milling operations in a single setup ensures excellent precision and accuracy. Components produced using needle turn-mill machining exhibit tight tolerances, precise dimensions, and consistent quality.
Increased Efficiency: Needle turn-mill combination machining offers increased efficiency by reducing material handling and eliminating the need for separate machining operations. This streamlines the production process, minimizes idle time, and optimizes workflow, leading to higher productivity.
Improved Surface Finish: The integrated turning and milling capabilities of needle turn-mill machining allow for superior surface finish on components. This eliminates the need for additional finishing operations, resulting in time and cost savings.
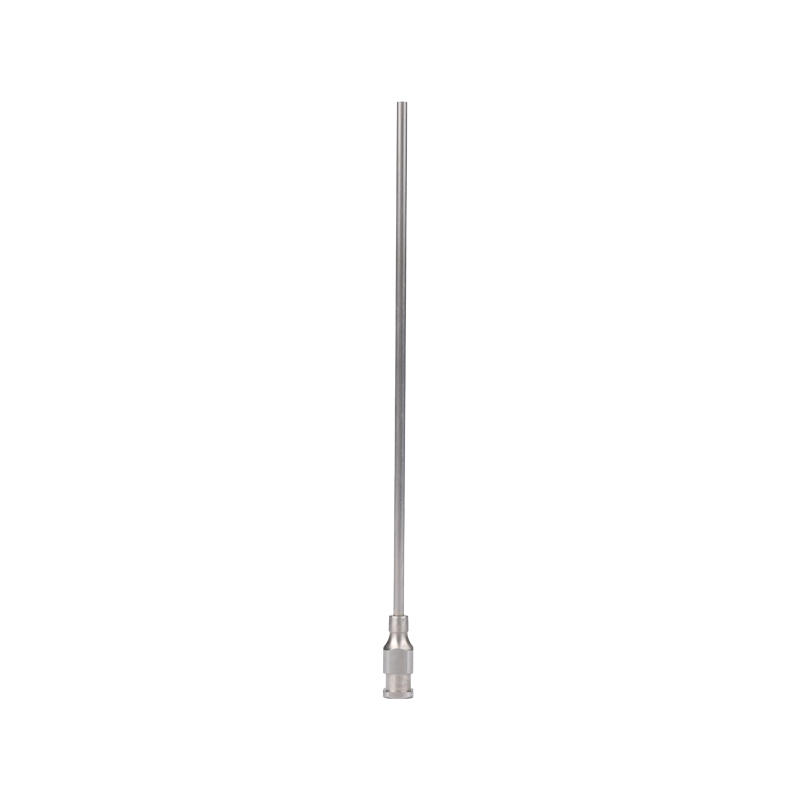
Applications:
Medical and Dental Devices: Needle turn-mill combination machining is extensively used in the production of medical and dental devices. It enables the manufacturing of intricate components, such as surgical instruments, dental implants, and orthopedic implants, with high precision and complex geometries.
Aerospace and Defense: The aerospace and defense industries benefit from needle turn-mill machining for the production of critical components, including turbine blades, engine parts, and aerospace fasteners. The technique allows for the creation of complex features and the machining of materials with high strength and heat resistance.
Automotive Industry: Needle turn-mill machining plays a crucial role in the automotive industry for manufacturing components like crankshafts, camshafts, transmission parts, and valves. The technique enables efficient production of these high-precision components, ensuring their accuracy and functionality.
Electronics and Communication: Precision machining is vital in the electronics and communication sectors for producing components like connectors, housings, and specialized connectors. Needle turn-mill combination machining enables the production of intricate features and precise dimensions required in these applications.
General Engineering: Needle turn-mill machining finds applications in various general engineering industries, including tooling, prototyping, and small batch production. It allows for the efficient production of custom components, reducing lead times and overall costs.
In conclusion, needle turn-mill combination precision machining offers numerous benefits, including versatility, reduced setup time, enhanced precision, increased efficiency, and improved surface finish. It finds applications across diverse industries, including medical, aerospace, automotive, electronics, and general engineering. By leveraging the capabilities of needle turn-mill combination machining, manufacturers can achieve high-quality components with complex features while optimizing productivity and cost-effectiveness.