When it comes to industrial applications, even the smallest components can have a big impact on the overall performance of a machine or system. This is especially true when it comes to nuts, which are used to secure bolts and other fasteners in place. While standard nuts may be suitable for many applications, there are times when non-standard precision nuts are necessary to ensure optimal performance and safety.
So what are non-standard precision nuts, and why are they important? We will explore the basics of these specialized nuts and their use in industrial applications.
What are Non-Standard Precision Nuts?
Non-standard precision nuts are nuts that are designed to meet specific requirements that cannot be met with standard nuts. These nuts may have unique shapes, sizes, or materials that make them better suited for particular applications. They may also be designed with tighter tolerances than standard nuts, allowing for more precise and secure fastening.
Examples of non-standard precision nuts include flange nuts, nylon insert nuts, and self-locking nuts. Flange nuts are designed with a wide flange at the base, which provides a larger bearing surface and distributes the load more evenly. Nylon insert nuts have a nylon ring embedded in the threads, which helps prevent loosening due to vibration. Self-locking nuts, as the name suggests, are designed to lock in place and prevent loosening without the need for additional locking devices.
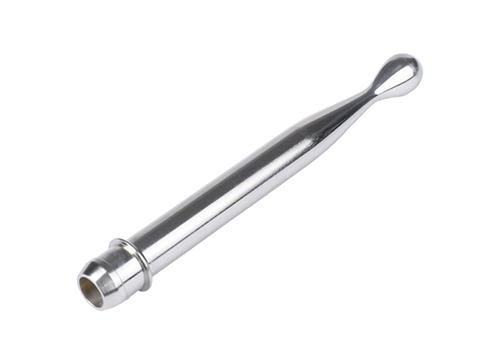
Why are Non-Standard Precision Nuts Important?
Non-standard precision nuts are important because they can improve the performance and safety of industrial systems. By using nuts that are specifically designed for a particular application, engineers can ensure that fasteners are securely and accurately fastened, reducing the risk of failure due to loosening or breakage. This is especially important in high-stress applications, such as automotive and aerospace engineering, where the consequences of fastener failure can be catastrophic.
In addition to their safety benefits, non-standard precision nuts can also improve the overall performance of industrial systems. By using nuts that are designed to meet specific requirements, engineers can optimize the performance of fasteners and minimize the risk of wear and tear over time. This can help extend the lifespan of machines and systems, reducing the need for maintenance and repairs.
In conclusion, non-standard precision nuts are a critical component in many industrial applications. By providing a greater level of precision and security than standard nuts, they can help improve the safety and performance of machines and systems. When selecting nuts for a particular application, it is important to consider the specific requirements and to choose nuts that are designed to meet those needs. By doing so, engineers can ensure that their systems operate reliably and efficiently over the long term.